Propeller, screw propeller A revolving screw-like device that drives the ship. The screwtype propeller consists of a hub and blades, all spaced at equal angles about the axis. When the blades are integral with the hub, the propeller is known as a solid propeller. When the blades are separately cast and secured to the hub by studs, the propeller is known as a built-up propeller.
I am getting ready to drill the prop shaft hole into a new keel. I plan to use the strut as a guide but I will first need to make (or have made)a bushing that will fit into the strut to secure the drill bit shaft and then fabricate an extended drill bit with a 1.5' bit.
The face (or pressure face) is the afterside of the blade when the ship is moving ahead. The back (or suction back) is the surface opposite the face. As the propeller rotates, the face of the blade increases pressure on the water to move it in a positive astern movement. The tip of the blade is the most distant from the hub. The root of the blade is the area where the blade joins the hub. The leading edge is the edge that cuts water first when the ship is going ahead.
The trailing edge (also called the following edge) is opposite the leading edge. A rake angle exists when the tip of the propeller blade is not precisely perpendicular to the axis (hub). The angle is formed by the distance between where the tip really is (forward or aft) and where the tip would be if it were in a perpendicular position.
A screw propeller may be generally classified as either fixed pitch or controllable pitch. The pitch of a fixed-pitch propeller cannot be altered during the operation. The pitch of a controllable-pitch propeller can be changed at any time, subject to bridge or engineroom control. The controllable-pitch propeller can reverse the direction of a ship without requiring a change of direction of the drive shaft. The blades are mounted so that each one can swivel or turn on a shaft that is mounted in the hub.
The thrust and torque of a propeller are created by the pressure differences on either side of the blades, which is related to relative velocity and blade geometry. The relative velocity is a function of the rotational speed (and radius) and the speed of water in the ship, s wake.
Reducing the propeller speed and increasing its diameter also increases the efficiency. In 1997, the heaviest propeller ever manufactured as single castings was supplied by Stone Manganese Marine. The six-bladed fixed pitch propeller was designed to absorb 65.9 MW, it has a diameter of 8950 mm and weighs 93.5 tonnes. Adjustable bolted propeller (ABP) – Similar in concept to a standard controllable pitch propeller, the ABP is based on a hollow hub with blades bolted to it from the inside. In service, the slotted holes on the hub allow the blade pitch angle to be adjusted to compensate for long-term variations in hull resistance. If the propeller is damaged, individual blades can be replaced without drydocking, and only spare blades have to be stocked rather than a bulky monobloc propeller.
Assembled propeller, built-up propeller – A propeller cast in more than one piece. In general, built-up propellers have the blades cast separately and fixed to the hub by a system of bolts and studs. CLT propeller – The contracted and loaded tip propellers, developed by Spanish company Sistemar in the late 1980s: screw propellers with important load at the blade tips due to the fitting of end plates at the blade tips. As well as a higher efficiency, CLT propeller also offers lower noise and vibration, lower fuel consumption and better.
Contra-rotating propellers (CRP) – see - – A propeller with a mechanism in the propeller hub that can be operated remotely to change the setting from a maximum design ahead pitch to a maximum design astern pitch. The pitch can be changed while the propeller rotates and develops thrust within these limits, or the pitch can be maintained at any intermediate setting for continuous operation. CP propellers are almost standard requirements on ferries and cruise liners where their handiness in manoeuvring and compatibility with highly-skewed blades for noise and vibration reduction is important. Applying full astern power on a highly-skewed FP screw can lead to stress problems, whereas the CP type, turning always in the same way and achieving astern thrust by pitch reversal, avoids problems. Ducted propeller, shrouded propeller – The propeller placed in a duct, i.e. A ring with a cross section that has a wing-like profile. The duct offers protection to the propeller blades and contributes to the thrust generated by the propeller.
The same amount of thrust can be generated from a propeller of smaller diameter, making it a suitable solution for small-draught vessels. – Propeller with blades rigidly attached to the hub. High skew propeller – A propeller of more than 25°C. A high skew blades are applied to suppress cavitation-induced pressure impulses. By skewing the blade, it is possible to reduce the vibration level to less than 30% of an unskewed design. The skew distribution is of the “balanced” type, which means that the blade chords at the inner radii are moved forward, while at the outer radii the cords are skewed aft. As the skew does not affect the propeller efficiency, it is a standard design on vessels where low vibration levels are required. Keyless propeller – A fixed pitch propeller that is press-fitted on the shaft cone.
No keyway with its stress concentration is present. Solid propeller – A propeller (including hub and blades) cast in one piece. Surface piercing propeller – A propeller that is positioned so the passes right through the propeller hub. Each propeller blade is out of the water for half of every revolution. The main reasons for using a surface piercing propulsion system are better propeller efficiency, reduced appendage drag, lack of cavitation and shallow draft.
This article needs additional citations for. Unsourced material may be challenged and removed. (June 2010) A drive shaft, driveshaft, driving shaft, propeller shaft ( prop shaft), or Cardan shaft is a mechanical component for transmitting and rotation, usually used to connect other components of a that cannot be connected directly because of distance or the need to allow for relative movement between them.
As torque carriers, drive shafts are subject to and, equivalent to the difference between the input torque and the load. They must therefore be strong enough to bear the stress, while avoiding too much additional weight as that would in turn increase their.
To allow for variations in the alignment and distance between the driving and driven components, drive shafts frequently incorporate one or more, or, and sometimes a. Contents. History The term drive shaft first appeared during the mid 19th century. In Stover's 1861 patent reissue for a, the term is used to refer to the belt-driven by which the machine is driven. The term is not used in his original patent. Another early use of the term occurs in the 1861 patent reissue for the Watkins and Bryson horse-drawn.
Here, the term refers to the shaft transmitting power from the machine's wheels to the gear train that works the cutting mechanism. In the 1890s, the term began to be used in a manner closer to the modern sense. In 1891, for example, Battles referred to the shaft between the transmission and driving of his as the drive shaft, and Stillman referred to the shaft linking the crankshaft to the rear axle of his as a drive shaft.
In 1899, Bukey used the term to describe the shaft transmitting power from the wheel to the driven machinery by a in his. In the same year, Clark described his Marine Velocipede using the term to refer to the gear-driven shaft transmitting power through a to the propeller shaft. Crompton used the term to refer to the shaft between the transmission of his steam-powered of 1903 and the driven axle. The pioneering automobile industry company, was the first to use a drive shaft in a gasoline-powered car.
Built in 1901, today this vehicle is in the collection of the Institution. Automotive drive shaft Vehicles An may use a longitudinal shaft to deliver power from an engine/transmission to the other end of the vehicle before it goes to the wheels. A pair of short drive shafts is commonly used to send power from a central, or to the wheels.
Main article: In vehicles, a longer drive shaft is also required to send power the length of the vehicle. Two forms dominate: The with a single and the more common with two or more joints. This system became known as after the automobile company patented it. Most of these vehicles have a and (or transmission) mounted directly on the engine, with a drive shaft leading to a final drive in the rear axle.
When the vehicle is stationary, the drive shaft does not rotate. Some vehicles (generally sports cars, most commonly or ), seeking improved weight balance between front and rear, use a rear-mounted. In some non-Porsche models, this places the clutch and transmission at the rear of the car and the drive shaft between them and the engine. In this case the drive shaft rotates continuously with the engine, even when the car is stationary and out of gear. However, the Porsche 924/944/928 models have the clutch mounted to the back of the engine in a bell housing and the drive shaft from the clutch output, located inside of a hollow protective torque tube, transfers power to the rear mounted transaxle (transmission + differential).Thus the Porsche driveshaft only rotates when the rear wheels are turning as the engine-mounted clutch can decouple engine crankshaft rotation from the driveshaft. So for Porsche, when the driver is using the clutch while briskly shifting up or down (manual transmission), the engine can rev freely with the driver's accelerator pedal input, since with the clutch disengaged, the engine and flywheel inertia is relatively low and is not burdened with the added rotational inertia of the driveshaft. The Porsche torque tube is solidly fastened to both the engine's bell housing and to the transaxle case, fixing the length and alignment between the bell housing and the transaxle and greatly minimizing rear wheel drive reaction torque from twisting the transaxle in any plane.
A drive shaft connecting a rear differential to a rear wheel may be called a half-shaft. The name derives from the fact that two such shafts are required to form one. Early automobiles often used or mechanisms rather than a drive shaft.
Some used electrical generators and motors to transmit power to the wheels. Front-wheel drive In, the term 'drive shaft' is restricted to a transverse shaft that transmits power to the wheels, especially the front wheels. A drive shaft connecting the gearbox to a rear differential is called a propeller shaft, or prop-shaft. A prop-shaft assembly consists of a propeller shaft, a and one or more. Where the engine and axles are separated from each other, as on and vehicles, it is the propeller shaft that serves to transmit the drive force generated by the engine to the axles.
Several different types of drive shaft are used in the automotive industry:. One-piece drive shaft. Two-piece drive shaft.
Slip-in-tube drive shaft The slip-in-tube drive shaft is a new type that improves crash safety. It can be compressed to absorb energy in the event of a crash, so is also known as a collapsible drive shaft.
Four wheel and all-wheel drive These evolved from the front-engine rear-wheel drive layout. A new form of transmission called the transfer case was placed between transmission and final drives in both axles. This split the drive to the two axles and may also have included reduction gears, a dog clutch or differential. At least two drive shafts were used, one from the transfer case to each axle. In some larger vehicles, the transfer box was centrally mounted and was itself driven by a short drive shaft.
In vehicles the size of a, the drive shaft to the front axle is noticeably shorter and more steeply articulated than the rear shaft, making it a more difficult engineering problem to build a reliable drive shaft, and which may involve a more sophisticated form of universal joint. Modern light cars with (notably or the ) may use a system that more closely resembles a front-wheel drive layout. The transmission and final drive for the front axle are combined into one housing alongside the engine, and a single drive shaft runs the length of the car to the rear axle. This is a favoured design where the torque is biased to the front wheels to give car-like handling, or where the maker wishes to produce both four-wheel drive and front-wheel drive cars with many shared components. Research and development The automotive industry also uses drive shafts at testing plants. At an a drive shaft is used to transfer a certain speed or torque from the to a. A 'shaft guard' is used at a shaft connection to protect against contact with the drive shaft and for detection of a shaft failure.
At a transmission test stand a drive shaft connects the prime mover with the transmission. Motorcycle drive shafts. The exposed drive shaft on BMW's first motorcycle, the Drive shafts have been used on since before WW1, such as the Belgian from 1903 and the Stellar motorcycle of 1912. As an alternative to and drives, drive shafts offer long-lived, clean, and relatively maintenance-free operation. A disadvantage of shaft drive on a motorcycle is that, or similar is needed to turn the power 90° from the shaft to the rear wheel, losing some power in the process. Has produced shaft drive motorcycles since 1923; and have built shaft-drive since the 1960s.
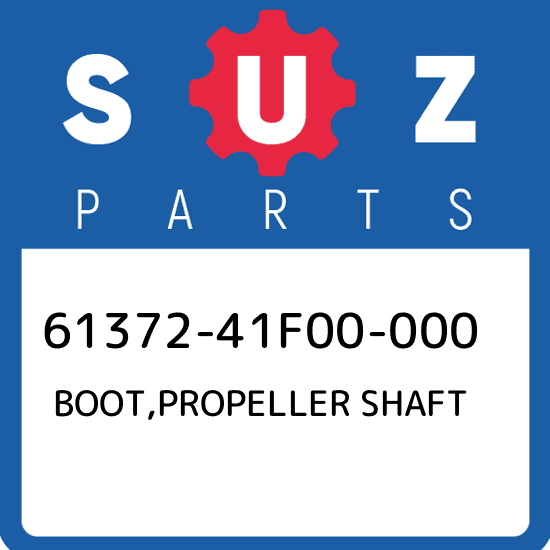
The British company, and the major Japanese brands, and, have produced shaft drive motorcycles. Motorscooters type A up to type LD were shaft-driven the NSU Prima scooter was also shaft-driven Motorcycle engines positioned such that the are often used for shaft-driven motorcycles. This requires only one 90° turn in power transmission, rather than two. Bikes from Moto Guzzi and BMW, plus the and all use this engine layout.
Motorcycles with shaft drive are subject to where the chassis climbs when power is applied. This effect, which is the opposite of that exhibited by chain-drive motorcycles, is counteracted with systems such as BMW's, Moto Guzzi's and Kawasaki's. Marine drive shafts On a power-driven ship, the drive shaft, or propeller shaft, usually connects the transmission inside the vessel directly to the, passing through a or other seal at the point it exits the. There is also a, a bearing to resist the axial force of the propeller. As the rotating propeller pushes the vessel forward, any length of drive shaft between propeller and thrust block is subject to, and when going astern to. Except for the very smallest of boats, this force isn't taken on the gearbox or engine directly.
Cardan shafts are also often used in marine applications between the transmission and either a propeller gearbox or waterjet. The portion of the prop shaft which connects directly to the propeller is known as the tail shaft. Locomotive drive shafts. The rear drive shaft, crankshaft and front drive shaft of a The, and locomotives, all introduced in the late 19th century, used to couple power from a centrally mounted multi-cylinder engine to each of the supporting the engine. On each of these, one end of each drive shaft was coupled to the driven truck through a while the other end was powered by the, or another truck through a second universal joint. A quill drive also has the ability to slide lengthways, effectively varying its length. This is required to allow the bogies to rotate when passing a curve.

Cardan shafts are used in some (mainly diesel-hydraulics, such as ) and some (e.g. They are also widely used in. Drive shafts in bicycles. A The drive shaft has served as an alternative to a chain-drive in for the past century, never becoming very popular. A (or 'Acatane', from an early maker) has several advantages and disadvantages: Advantages. Drive system is less likely to become jammed. The rider cannot become dirtied from chain grease or injured by 'chain bite' when clothing or a body part catches between an and a sprocket.
Propeller Shaft Packing
Lower maintenance than a chain system when the drive shaft is enclosed in a tube. More consistent performance. Dynamic Bicycles claims that a drive shaft bicycle can deliver 94% efficiency, whereas a chain-driven bike can deliver anywhere from 75-97% efficiency based on condition. Disadvantages.
A drive shaft system weighs more than a chain system, usually 0.5–1 kg (1–2 lb) heavier. Many of the advantages claimed by drive shaft's proponents can be achieved on a chain-driven bicycle, such as.
Use of lightweight gears with a high number of ratios is impossible, although can be used. Wheel removal can be complicated in some designs (as it is for some chain-driven bicycles with hub gears). Drive shaft production Nowadays new possibilities exist for the production process of drive shafts. The production process is gaining popularity for the creation of drive shafts. Several companies in the automotive industry are looking to adopt this knowledge for their high volume production process. See also.
References. Stover, Improvement in Wood-Planing Machines, May 21, 1861. Stover, Planing Machine, Dec.
18, 1860, 1861. John DeLancy Watkins and Robert Bryson, Mowing Machines, July 23, 1861. Battles, Locomotive, June 30, 1891. Walter Stillman, Bicycle, July 21, 1891.
Bukey, Horse-Power, Aug. Charles Clark, Marine Velocipede, U.S. Patent 637,547, Nov. Charles Crompton, Motor-Vehicle, January 1903.
National Museum of American History. Retrieved November 19, 2017. Cambridge Lambretta Workshop.
Retrieved August 26, 2016. Retrieved August 26, 2016.